A dewatering screw press that separates Liquids from solids. A screw press can be used in place of a belt press or a filter paper.
It is a slow moving device that accomplishes dewatering by continuous gravitational drainage. Screw presses are often used for materials that are difficult to press, for example those that tend to pack together. The screw press squeezes the material against a screen or filter and the liquid is collected through the screen for collection and use.
Design of screw press
Most screw presses can have dilute materials pumped directly into the screw press, although pre-thickening sometimes improves the performance of the press. This is typically done with a static or side hill screen, a rotating drum screen, belt press, or a gravity table
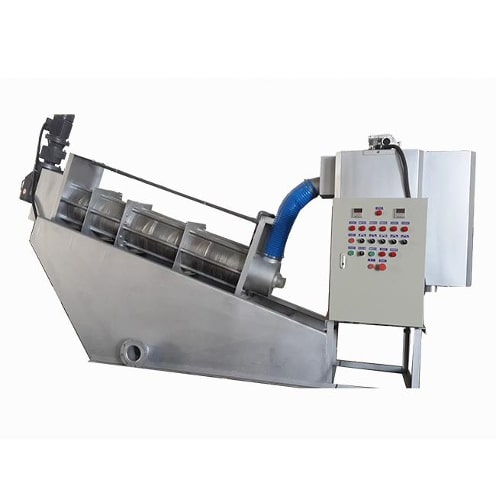
Classification
There are two major kinds of screw presses of this design.
• Expellers :- Oil expellers are used to squeeze the fat out of canola (rape seeds), and other oil. The expeller works by exerting extremely high pressures which convert the fat in seeds into a liquid oil. Once the oil is liquefied the oil flows through the screen and is collected.
• Removal of free liquid :- Screw presses that are used to free liquid from material are commonly used in the pulp and paper industries, and also within the chemical Industry
Capacity
The specific details of the design of a screw press depend on the material however. The configurations, screw speeds, screens for maximum outlet consistency, including an excellent capture rate vary per material. Most screw presses are designed to feed material that has a 40-60% water make up. The length and diameter ratio of the screw press also depends on the material. The range of the capacity of a screw press.
Drive
Larger presses use a foot-mounted gearbox while smaller presses use a hollow-shaft gearbox. Currently, nearly all presses are driven by electric motors due to their reliable and low cost frequency drives. The electric motors replaced the previously popular hydraulic motor drives. A vertical design was popular in the 1800s but they are no longer made. Most screw presses are currently built with the screws in a horizontal configuration. One newer version uses an angled screw design to reduce floor footprint and press cake moisture.
Working of dewatering screw press
Compression is created within the screw press by increasing the inner shaft diameter of the screw. This compression can also be achieved tightening the separation of the flights of the screw.
Another way to achieve compression is to place a cone at the point of discharge. This can also be called a choke, stopper, or door. In many designs it is bolted into a fixed position, making a fixed, smaller opening which the material must pass through. More commonly found however, the screw press has the cone pushed into the point of discharge via a hydraulic or air cylinder.
The sludge is lifted to the mixing tank by the sludge pump. At this time, the dosing pump also quantitatively transports the liquid to the mixing tank, and the stirring motor drives the entire mixing system to combine the sludge with the liquid. Perform sufficient mixing to produce alum. When the liquid level reaches the upper level of the liquid level sensor, the liquid level sensor will get a signal at this time, so that the motor of the main body of the screw press starts to press and filter the sludge. Under the action of the screw shaft, the sludge is lifted to the sludge outlet step by step, and the filtrate flows out from the gap between the fixed ring and the moving ring.
Automated dewatering screw press
Dewatering Press is a fully automated system capable of starting up, operating, and shutting down with no operator intervention. This is possible because the control panel is designed to control the operation of wasting sludge directly from the biological processor or clarifier, the automated polymer feed system, flocculation, dewatering, and any conveyors required to remove dewatered cake. Thus, all components of the dewatering system work together, automatically starting up, and shutting down as required.
Specialized types
Some other types of presses are vapor-tight presses, and twin-screw presses. Vapor-tight presses are used during the production of soybean protein concentrate (SPC), Twin-screw presses contain two overlapping compression screws. This is more complicated on a mechanical level because the screws must remain synchronized in order for them to work properly. These are often used for slippery materials and feature an internal shredding action.
Applications
• Pulp and paper industries
• Sewage disposal
• Food processing
• Chemical industry